TECHNOLOGY
Unveiling Hasactcind: The Next Big Thing in Technology
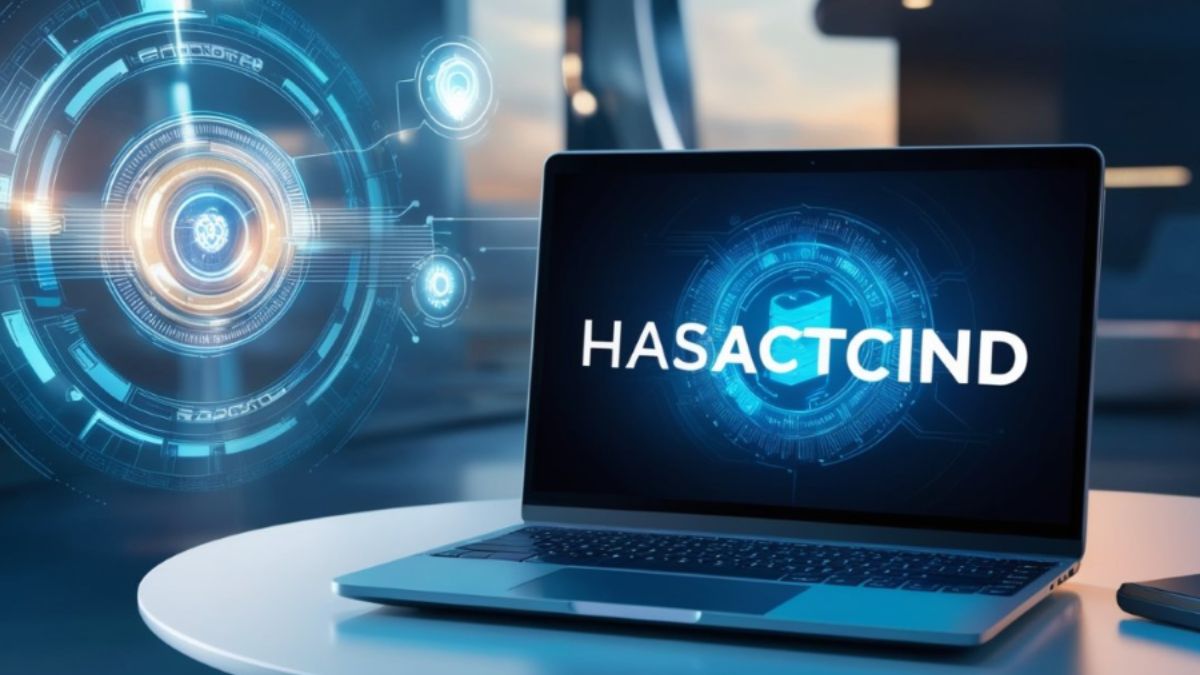
Welcome to the future of technology! If you haven’t heard about Hasactcind yet, you’re in for a treat. This innovative platform is creating waves across various sectors, promising to revolutionize how we interact with digital solutions. With its cutting-edge features and user-friendly interface, Hasactcind has quickly emerged as a game-changer in tech. As we embark on this exploration, prepare to uncover what makes Hasactcind stand out from the crowd and why it might just be the next big thing you’ve been waiting for!
What is Hasactcind and How Does it Work?
Hasactcind is an innovative technology that merges advanced algorithms with artificial intelligence. At its core, it aims to optimize processes across various sectors.
How does it work? Imagine a system that learns and adapts in real time. Hasactcind analyzes data streams, identifies patterns, and makes predictions based on user interactions. This self-learning capability sets it apart from traditional technologies.
The platform operates seamlessly by integrating with existing systems. Users can harness its power without overhauling their current infrastructure.
In essence, Hasactcind transforms raw data into actionable insights. It empowers businesses to make informed decisions swiftly and efficiently. As organizations embrace this cutting-edge solution, the potential for enhanced productivity becomes evident.
The Benefits of Using Hasactcind
Hasactcind offers a myriad of benefits that set it apart in the tech landscape. Its ability to streamline processes is one of its most appealing features. Users can expect increased efficiency, allowing teams to focus on creative and strategic tasks rather than mundane operations.
Moreover, Hasactcind enhances collaboration among team members. By providing real-time updates and centralized data access, it ensures everyone stays informed and engaged.
Security is another strong suit of Hasactcind. Built with robust encryption protocols, it safeguards sensitive information against potential breaches.
Additionally, the technology’s scalability makes it suitable for businesses of all sizes. Whether you’re a startup or an established corporation, you can tailor Hasactcind to fit your specific needs without significant overhauls.
The user-friendly interface simplifies onboarding for new users. This ease of use encourages adoption across departments and minimizes training time.
The Potential Impact on Different Industries
Hasactcind is poised to revolutionize various industries with its innovative capabilities. In healthcare, it could streamline patient data management, enhancing efficiency and accuracy in diagnoses.
Manufacturing might see increased automation through Hasactcind’s integration of AI and machine learning. This would lead to reduced operational costs and improved production timelines.
The retail sector stands to benefit from personalized customer experiences driven by the technology’s advanced analytics. Businesses can tailor their offerings based on real-time consumer insights.
In finance, Hasactcind may transform how transactions are processed, providing faster and more secure payment solutions. This could significantly reduce fraud risks while boosting confidence among users.
Education isn’t left behind either; interactive learning environments powered by Hasactcind can enhance student engagement. The potential for virtual classrooms makes education more accessible than ever before.
As these sectors adapt, we will likely witness a comprehensive shift towards smarter operations across the board.
How to Get Started with Hasactcind
Getting started with Hasactcind is simpler than you might think. First, visit the official website to gather essential resources and information.
Next, create an account. This step usually involves providing basic details like your name and email address. Once registered, you’ll gain access to tutorials and community support forums.
Familiarize yourself with the platform’s interface. Spend some time exploring its features and functionalities. The more comfortable you become, the easier it will be to harness its full potential.
Consider joining online communities or groups focused on Hasactcind. Engaging with other users can provide insights that enhance your learning experience.
Don’t hesitate to experiment! Practical application is key in mastering any new technology. Dive into projects that pique your interest; hands-on experience often leads to the best understanding of Hasactcind’s capabilities.
Comparing Hasactcind to Other Technologies
Hasactcind stands out in the tech landscape, offering features that often surpass traditional solutions. Unlike conventional platforms, it integrates multiple functionalities into a seamless experience. This allows for greater efficiency and user satisfaction.
When compared to older technologies, Hasactcind shines with its adaptability. Many legacy systems struggle to evolve with changing demands. In contrast, Hasactcind is designed for flexibility and rapid updates.
Moreover, while other tools may require extensive training or onboarding processes, Hasactcind prioritizes usability. Its intuitive interface ensures even non-technical users can navigate it easily.
The speed of deployment also sets Hasactcind apart. Other technologies often come with long setup times, whereas this innovative solution gets businesses up and running quickly without sacrificing performance.
In essence, comparing Hasactcind to existing technologies reveals significant advantages that could redefine industry standards moving forward.
Future Possibilities and Development Plans for Hasactcind
The future of Hasactcind holds immense potential. Developers are actively exploring new applications across various sectors. Innovative features are on the horizon, promising to enhance user experience and drive efficiency.
Research teams are focused on integrating artificial intelligence with Hasactcind. This combination could unlock advanced functionalities, making it even more adaptable. Imagine a tool that learns from user interactions, evolving with each use.
Collaboration is also key in its development plan. Partnerships with leading tech firms may pave the way for groundbreaking enhancements. These alliances can fuel creativity and expand capabilities.
Moreover, community feedback plays a significant role in shaping Hasactcind’s evolution. Engaging users in the development process ensures their needs are met effectively.
With ongoing research and ambitious goals, Hasactcind is poised to revolutionize how we approach technology in everyday life. Exciting times lie ahead as this platform continues to unfold its possibilities.
Conclusion
The rapid evolution of technology continues to surprise us, and Hasactcind is certainly at the forefront of this transformation. Its innovative capabilities and user-friendly interface make it a compelling option for individuals and businesses alike.
As we dive deeper into its functionalities, understanding how Hasactcind can fit into various sectors becomes crucial. From enhancing operational efficiencies in industries like healthcare to revolutionizing data management in finance, the applications seem limitless.
Getting started with Hasactcind doesn’t have to be daunting. With accessible resources and support communities emerging, users can easily navigate their way through implementation.
When compared to existing technologies, it’s clear why many are excited about Hasactcind’s potential. It stands out not just for its unique features but also for its adaptability across several fields.
Looking ahead, the future holds exciting possibilities for further development within Hasactcind’s framework. The continuous feedback loop from early adopters will likely shape its trajectory in profound ways.
The journey with Hasactcind has only just begun; those willing to embrace this new wave of innovation may find themselves at an advantage as they explore uncharted territories in technology.
TECHNOLOGY
PR Public Relation Guest Post Agency Guest Posting: A Modern Strategy for Brand Credibility and Digital Authority
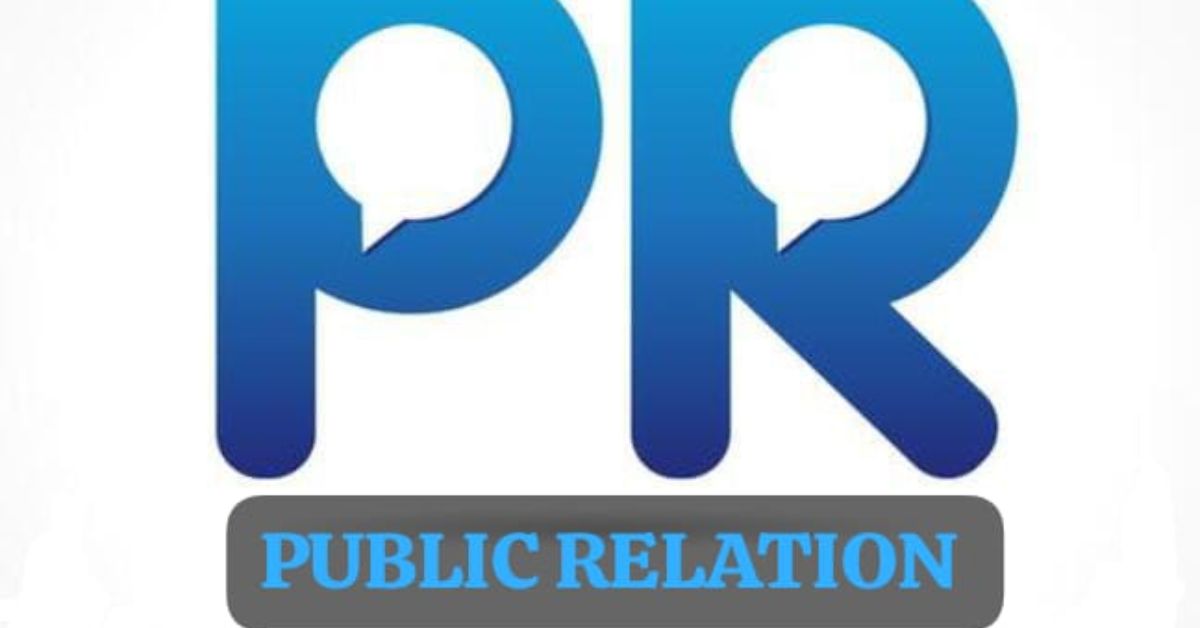
In the digital age, where online visibility directly influences brand success, PR Public Relation Guest Post Agency (PR) has evolved from traditional press coverage and event management into a more dynamic, content-driven practice. One of the most effective strategies at the intersection of modern PR and digital marketing is guest posting.
Guest posting—publishing content on external, high-authority websites—not only supports link-building and SEO goals but also plays a critical role in shaping public perception, building thought leadership, and enhancing brand trust. For professionals, startups, and enterprises alike, integrating guest posting into a PR Public Relation Guest Post Agency plan has become an indispensable tactic for long-term brand positioning.
Understanding Guest Posting in the PR Context
Traditionally, PR focused on managing the flow of information between an organization and the public. It was about getting stories into newspapers, interviews on radio, or features on TV. However, the digital shift has changed how audiences consume content. People now turn to blogs, digital publications, industry websites, and social media for insights and updates.
This shift has broadened the definition of PR. It’s no longer limited to media relations—it includes content marketing, thought leadership, influencer partnerships, and most notably, guest posting on authoritative platforms.
Guest posting in PR involves writing and publishing valuable, non-promotional content on websites that align with your industry or target audience. The goal is not just exposure, but positioning your brand or spokesperson as a credible authority, while also subtly driving traffic and improving SEO rankings through contextual backlinks.For more information please contact this email: toppublicrelation@gmail.com
Why Guest Posting Matters for Public Relations
Here’s why guest posting is a vital tool for modern PR Public Relation Guest Post Agency:
1. Establishing Thought Leadership
Credibility is currency in the digital world. When a company’s executive or representative contributes an article to a respected industry site, it reinforces their position as a thought leader. Readers trust websites they follow, so your message carries more weight when published externally than when posted on your brand blog.
Guest posting allows PR professionals to tell their story proactively, providing meaningful commentary on industry trends, innovations, and challenges—before the competition does.
2. Controlling the Narrative
Guest posts offer a powerful form of narrative control. Instead of relying on third-party journalists to interpret your press releases or statements, you get to shape your message directly. With guest posting, your voice becomes the official voice of record, helping prevent misrepresentation or dilution of the message.
This control is especially critical during product launches, rebranding efforts, crisis management, or shifts in company strategy. A well-placed article on a trusted platform can clarify your intentions, inspire confidence, and reduce misinformation.
3. Link Building and SEO
From a technical PR standpoint, backlinks are one of the strongest ranking factors in search engine algorithms. Guest posts are a natural way to earn these links, especially from high-authority domains.
When your content is published on a DA 70+ website and links back to your homepage or landing page with relevant anchor text, it improves your search engine visibility, increases referral traffic, and amplifies your online authority.
PR isn’t just about being seen in the news—it’s about being found when your audience is searching. Guest posting bridges this gap effectively.
How to Use Guest Posting Strategically in PR Campaigns
For a guest posting strategy to support your PR goals, it must be executed with precision. Below are key steps to follow:
1. Define Your PR Objectives
Are you looking to boost brand awareness? Rebuild reputation? Introduce a new product? Increase executive visibility? Your goals will shape the types of websites you target and the content themes you develop.
2. Target the Right Platforms
It’s not just about quantity—it’s about quality. Target websites that:
- Have high Domain Authority (DA)
- Are relevant to your industry or niche
- Have engaged audiences
- Accept guest contributions
Examples include platforms like Entrepreneur, Inc., Business Insider, or niche-specific blogs and publications with loyal readerships.
3. Create Valuable, Non-Promotional Content
Guest posts should never be overt sales pitches. Focus on educating, informing, or solving a problem. Showcase your expertise subtly while delivering genuine value. Content that reads like an article in Forbes, not an ad, will resonate better and be more widely accepted.
4. Craft a Strong Author Bio
The author bio is where you can place a branded backlink and provide credentials. It should reflect the authority of the spokesperson and give readers a clear reason to trust or follow the company.
5. Track Impact and ROI
Track metrics like:
- Referral traffic from guest post backlinks
- Organic keyword rankings
- Brand mentions and citations
- Media coverage triggered by guest post visibility
- Lead generation and conversions
These indicators help measure the real PR impact of guest posting campaigns.
Best Practices for Public Relations Guest Posting
To maximize the benefits of guest posting within your PR strategy, keep these best practices in mind:
- Personalize your outreach:Avoid mass-pitching editors. Tailor your pitches to show familiarity with the site’s tone and topics.
- Stay consistent:Publish regularly, not sporadically. Consistency builds recognition.
- Update your posts:Offer evergreen content, but revisit and refresh when necessary.
- Leverage social media:Share guest posts across LinkedIn, X (Twitter), and Facebook to extend reach.
- Build relationships with editors:Guest posting can open doors to broader PR opportunities like interviews, collaborations, and features.
The Future of PR: Content-Led Brand Building
The era of PR being reliant solely on press releases and journalists is long gone. Brands are now media companies, and their content is their currency. Guest posting fits perfectly into this model, offering a direct channel to communicate with audiences, control messaging, and build digital authority.
In the coming years, we’ll continue to see the fusion of PR, SEO, and content marketing. Agencies and internal teams that understand how to craft compelling guest posts and secure premium placements will lead the conversation in their industries.
Moreover, as AI and automation evolve, the human element—trust, credibility, and storytelling—will matter more than ever. Guest posting remains a tool where human perspective and professional authority can truly shine.
Conclusion
PR Public Relation Guest Post Agency today is a multidimensional effort that includes strategic content distribution, relationship-building, and digital visibility. Guest posting is a core pillar of this strategy—one that not only enhances online authority and improves SEO but also builds real, lasting brand trust.
Whether you’re launching a brand, repositioning a business, or strengthening your digital footprint, guest posting should be an integral part of your PR toolkit. It delivers value beyond a single post—contributing to your brand’s voice, influence, and credibility in a way few other tactics can.
TECHNOLOGY
Why Every E-commerce Store Needs an AI Chatbot Development Company in 2025?
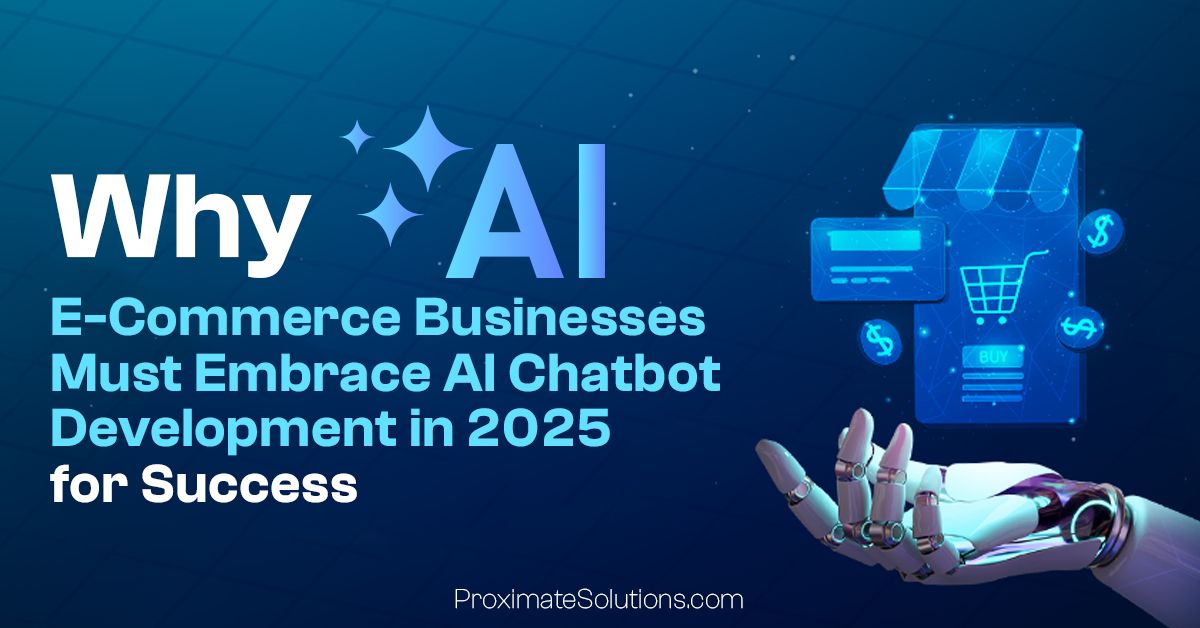
The Future of E-commerce Is AI-Driven
In 2025, customer expectations are evolving faster than ever. E-commerce brands are now competing on speed, personalization and round-the-clock availability. That’s where an AI Chatbot Development Company steps in. With AI transforming customer service, these companies enable businesses to deliver smarter, faster and more human-like support.
Today, 80% of retail and e-commerce businesses are either using or planning to implement AI chatbots. Additionally, the AI chatbot market in e-commerce is expected to reach $2.1 billion by 2032, driven by its ability to streamline operations, reduce costs and boost customer satisfaction.
Furthermore, an AI Chatbot Development agency equips brands with intelligent, automated support systems trained to sound like their brand, respond instantly and retain customer loyalty. Thus, for any business owner tired of answering repetitive questions, chatbots offer the perfect solution.
What Does an AI Chatbot Development Company Offer?
An AI Chatbot Development agency builds smart virtual assistants tailored for e-commerce platforms. These chatbots perform essential functions while saving businesses time and money. Additionally, here’s what they typically offer:
24/7 Customer Support: AI chatbots are always available to help since they never sleep.
Product Recommendations: They personalize suggestions based on browsing behavior.
Order Tracking: Customers get real time updates without contacting human agents.
Multilingual Communication: Breaks language barriers for global markets.
Cart Recovery Campaigns: Reminds customers to complete purchases.
Instant Query Handling: From FAQs to refund policies, bots manage it all efficiently.
Thus, by partnering with a professional AI Chatbot Development Company, brands receive custom built solutions that align with their tone, branding and goals.
How AI Chatbots Are Transforming E-commerce Customer Support
E-commerce customers expect quick responses and relevant solutions. That’s where AI chatbots shine. Additionally, these bots are trained on a company’s knowledge base, FAQs and customer workflows, providing accurate answers instantly. Thus, here’s how they transform customer support
Faster Response Times: Chatbots answer within seconds, reducing wait time.
Scalability: Handle thousands of conversations without needing more staff.
Brand Consistency: They reflect your tone and speak like your business.
Reduced Human Errors: AI systems ensure consistent and factual responses.
Lower Support Costs: Businesses save up to 30% in customer service costs.
Furthermore, a trusted and experienced AI Chatbot Development Company like Proxmate Solutions ensures bots can grow with your business and adapt to changing customer needs. That flexibility is very important in a competitive market.
Why Every E-commerce Business Needs AI Chatbots in 2025
Customer behavior in 2025 demands innovation. Today’s consumers use voice search, prefer messaging over calling and expect instant gratification. AI chatbots meet these demands by integrating seamlessly into websites, apps and messaging platforms.
Furthermore, here are the top reasons to invest in chatbot development
Consumer Trends: Most customers prefer messaging platforms over emails or calls.
Conversion Boost: Bots help customers check out which boosts sales.
Lead Qualification: Chatbots gather user data and segment customers.
Customer Retention: Personalized responses improve satisfaction and loyalty.
Voice Search Optimization: Modern bots work well with voice commands.
This is why hiring an AI Chatbot Development Company is no longer optional. It’s a strategic necessity.
Why Choose Proximate Solutions as Your AI Chatbot Development Company?
With over 20+ years of experience, Proximate Solutions stands out among AI chatbot providers. They are committed to quality, innovation and results-driven services. Whether you’re a startup or an established enterprise, their custom chatbot solutions fit businesses of all scales.
Reasons to hire Proximate Solutions
Proven Experience: Decades of expertise in AI and automation.
Sales-Focused Strategy: They build chatbots that convert, not just communicate.
Affordable Global Services: Competitive rates with top-tier service quality.
Always Up-To-Date: They embrace new AI trends to keep you ahead.
Custom Training: Their bots are trained on your brand tone, FAQs and workflows.
Furthermore, tired of answering repetitive customer queries? Proximate Solutions creates AI-powered chatbots that retain customer engagement, reduce response time and sound exactly like your brand.
Key Benefits of Hiring an AI Chatbot Development Company
Working with an AI Chatbot Development agency offers distinct advantages. Here are the key benefits that e-commerce businesses gain:
Increased Customer Satisfaction: Bots resolve issues quickly and accurately.
Boosted Efficiency: Agents can focus on complex cases while bots handle routine queries.
High ROI: Chatbots reduce support costs and drive conversions.
Brand Loyalty: Personalized interactions build stronger customer relationships.
Seamless Integration: Bots can be added to Shopify, WooCommerce, Magento and more.
Thus, choosing the right partner ensures you make the most of your AI investment. That’s where Proximate Solutions proves its value repeatedly.
A Look at the Future: AI Chatbots and Rising Expectations
By 2025, customers will expect businesses to be available 24/7, responsive and conversational. AI chatbot integration addresses all of these demands.
As the AI market grows, businesses that adopt early will have a competitive edge. AI-powered bots will not just assist but anticipate customer needs, becoming virtual shopping assistants.
Furthermore, future-ready e-commerce brands will use AI to:
- Predict customer preferences
- Handle high volume shopping events
- Improve post purchase engagement
- Offer hyper personalized support
Moreover, brands can successfully adjust to these developments with the help of professionals like Proximate Solutions. Their strategic approach to chatbot development ensures long term growth.
Conclusion: Build the Future of Customer Support Now
It’s very important to match customer expectations in the rapidly evolving world of e-commerce today. AI chatbots do more than answer questions; they build trust, drive sales and elevate brand experience. Thus, the businesses that recognize this shift and partner with an expert AI Chatbot Development Company will lead the way.
Furthermore, Proximate Solutions is one of the best choices to start this journey. With a proven track record, global reach and sales-focused strategies, they help e-commerce stores thrive in the AI-powered era.
Thus, don’t let your brand fall behind. Invest in AI chatbot solutions that speak your brand’s language, serve your customers 24/7 and power your business into the future.
Frequently Asked Questions (FAQs)
- What is an AI Chatbot Development Company?
It’s a company that creates intelligent chatbots using artificial intelligence to automate customer support and sales processes.
- Why do e-commerce stores need AI chatbots in 2025?
Customer expectations demand instant responses and 24/7 support which AI chatbots provide efficiently.
- How much does it cost to hire an AI Chatbot Development Agency?
Costs vary, but companies like Proximate Solutions offer competitive pricing tailored to your business size.
- Can AI chatbots increase my e-commerce sales?
Yes. They assist during purchase decisions, offer upsells and remind customers to complete abandoned carts.
- Are AI chatbots compatible with Shopify or WooCommerce?
Absolutely. An experienced AI Chatbot Development agency can integrate bots into all major platforms.
- How do AI chatbots personalize customer experiences?
They use browsing history, previous orders and user preferences to offer tailored product suggestions.
- How secure is customer data with AI chatbots?
Top companies follow strict data protection protocols and ensure GDPR and CCPA compliance.
TECHNOLOGY
Using Dynamics 365 Customer Engagement to Build Stronger Customer Relationships
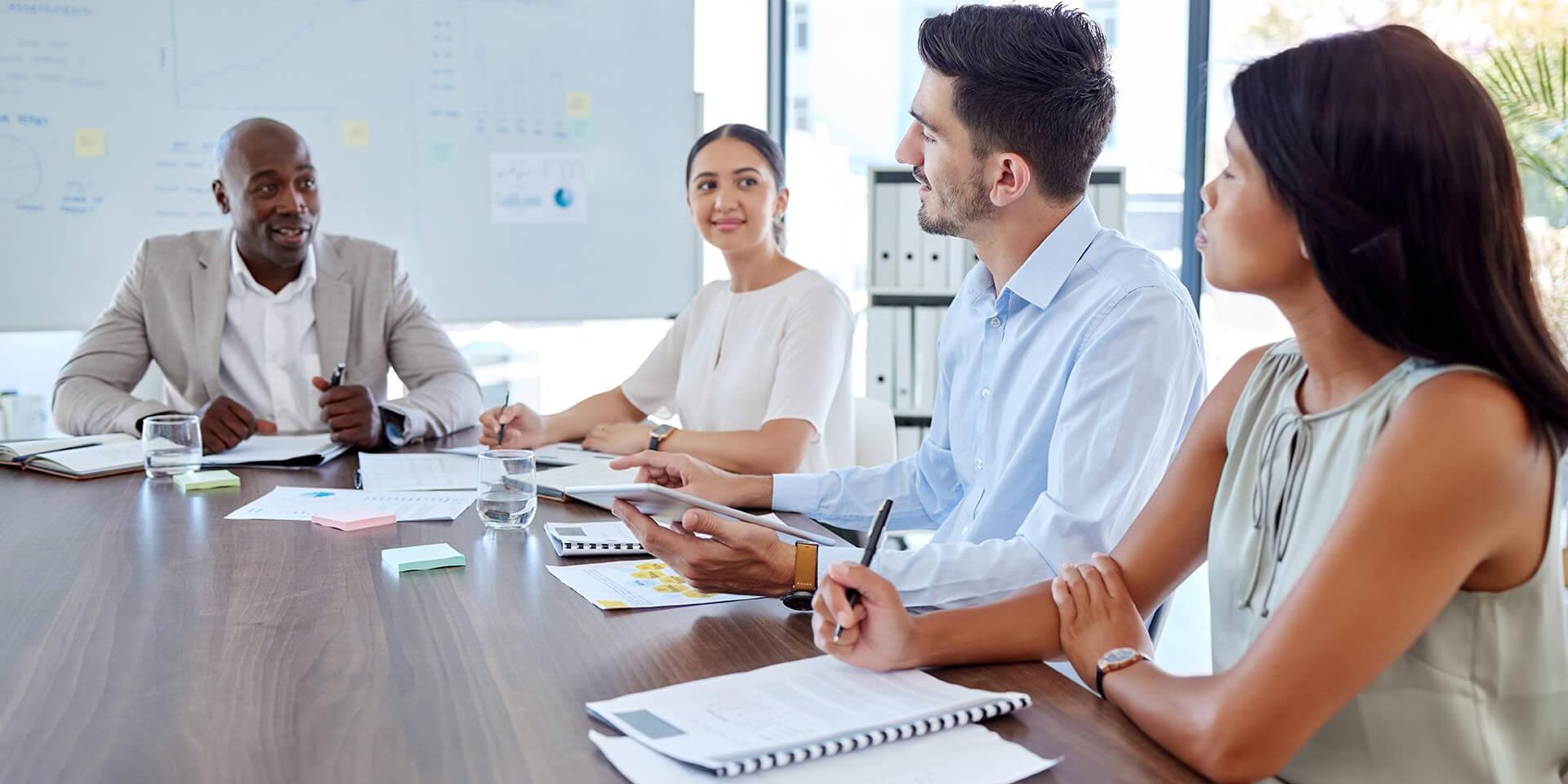
In today’s ultra-competitive business environment, having a great product or service is no longer enough. Customers expect personalized experiences, quick responses, and proactive engagement. The brands that stand out are the ones that truly understand their customers and build relationships that go beyond the transaction.
That’s where Dynamics Customer Engagement (part of Microsoft Dynamics 365) comes in. This powerful suite of applications helps businesses manage interactions and elevate every touchpoint—from sales and marketing to service and support.
In this post, we’ll explore how Dynamics 365 Customer Engagement enables businesses to build stronger customer relationships by unifying data, automating processes, and delivering personalized experiences.
What Is Dynamics Customer Engagement?
Dynamics 365 Customer Engagement (D365 CE) is a collection of applications within Microsoft’s Dynamics 365 ecosystem designed to manage customer-facing functions. These include:
- Sales
- Customer Service
- Marketing
- Field Service
- Project Service Automation
These apps help businesses gain a 360-degree view of customers, track interactions, automate follow-ups, and provide consistent, data-driven experiences at every customer journey stage.
Key ways Dynamics Customer Engagement builds stronger relationships
1. A Unified view of the customer
Nothing damages a relationship like fragmented communication. With Dynamics Customer Engagement, all customer data—past purchases, support tickets, email interactions, preferences—is unified in one place. This gives your teams complete visibility into who the customer is and what they need.
Sales, marketing, and service teams can all work from the same playbook. This ensures no customer falls through the cracks and every conversation feels informed and consistent.
2. Personalized Engagement at Scale
Customers want to feel understood, not marketed to. Dynamics Customer Engagement empowers you to deliver hyper-personalized experiences by leveraging AI-powered insights and behavioral data.
With dynamic segmentation in the marketing app, for example, you can send tailored messages based on a customer’s interests, buying history, or activity level. The sales team can use predictive insights to recommend the right next steps. Support agents get context about previous issues so they don’t have to ask customers to repeat themselves.
This level of personalization shows customers that you’re not just managing a database—you’re invested in the relationship.
3. Automated, Timely Interactions
Timeliness is key in maintaining strong relationships. Whether it’s a sales follow-up, service update, or birthday greeting, Dynamics Customer Engagement helps you automate communication without losing the human touch.
You can set up workflows to trigger emails, assign tasks, or escalate issues automatically. This ensures customers are always in the loop and feel valued, without overwhelming your team with manual follow-ups.
Marketing automation, in particular, lets you nurture leads with the right content at the right time, increasing trust and conversion rates.
4. Proactive Customer Service
Great relationships are built on trust, often from solving problems before they escalate.
With Dynamics Customer Engagement, your service teams can become proactive instead of reactive. Built-in dashboards and AI-driven insights can flag potential issues early, allowing you to reach out to customers before they complain.
The system can also suggest the next best actions, knowledge articles, or even automatically route cases to the most qualified agent. This reduces resolution time and boosts customer satisfaction.
5. Mobility and Accessibility
Today’s workforce is mobile, and so are customers. Dynamics CE is accessible across devices, ensuring that your team can engage with customers wherever they are—whether it’s on the sales floor, in the field, or working remotely.
Sales reps can pull up real-time customer data before a meeting. Service agents can respond to queries from a tablet. Field technicians can update job status on-site. That level of connectivity keeps your team aligned, informed, and ready to serve.
Real-World Example: Turning Data into Delight
Let’s say you run a mid-sized B2B company. You’ve been struggling with customer churn and inconsistent service experiences. By implementing Dynamics Customer Engagement, you’re able to:
- Sync sales, service, and marketing teams onto one platform
- Segment customers by industry and behavior
- Automate onboarding emails and product tips
- Flag inactive accounts for proactive outreach
- Equip support agents with detailed customer histories
Over six months, your churn rate drops, customer feedback improves, your team feels empowered, and most importantly, your customers feel like they matter because every interaction reinforces that belief.
Choosing the Right Dynamics CE Modules
Depending on your goals, you might not need the entire Dynamics suite. Here’s a quick guide:
- For Relationship Management & Sales: Start with Dynamics 365 Sales.
- For Personalized Marketing Campaigns: Use Dynamics 365 Marketing.
- For Omnichannel Customer Support: Go with Dynamics 365 Customer Service.
- For On-site Services: Consider Dynamics 365 Field Service.
Each module can work independently or as part of a connected solution, giving you flexibility as your business evolves.
Final Thoughts: Relationship-Building in the Digital Age
In an age where customers are bombarded with choices, loyalty comes down to how they feel about your brand. Do they feel heard? Understood? Valued?
Dynamics Customer Engagement helps answer those questions with a resounding “yes.” Combining unified data, intelligent insights, and personalized automation transforms how you connect with customers, from one-off transactions to long-term partnerships.
If building stronger relationships is a priority for your business—and it should be—investing in the right tools like Dynamics Customer Engagement isn’t just a tech decision. It’s a growth strategy.
-
TECHNOLOGY1 year ago
Elevating Game Day Eats: A Guide to Crafting Crowd-Pleasing Sliders
-
ENTERTAINMENT1 year ago
wave_of_happy_: Your Ultimate Guide
-
FASHION2 years ago
GPMsign Fashion: Redefining Style with Purpose
-
TECHNOLOGY1 year ago
Trader Joe’s Dayforce: Revolutionizing Workforce Management
-
FOOD1 year ago
Altador Cup Food Court Background: A Culinary Extravaganza Unveiled
-
SPORTS2 years ago
Score Chaser Sporting Clays: A Thrilling Pursuit of Precision
-
HOME IMPROVEMENT11 months ago
What Kitchen Renovation Companies Offer Beyond Basic Remodeling
-
NEWS1 year ago
Nyl2 Kemono: Unveiling the World