TECHNOLOGY
A Guide to Understanding Keyword Competition in SEO
When it comes to Search Engine Optimisation, keywords are key to getting your website seen. But it’s not just about choosing any keywords — it’s about choosing the right ones. Some keywords are much more influential than others. However, this might be a confusing area for many businesses and individuals. So, here’s our guide that explains keyword competition in detail for your SEO in Melbourne.
What is Keyword Competition?
Ranking high in search results for popular terms is a fierce battle. Many sites vie for top spots, leaving newcomers struggling to break through. Yet hidden gems exist – less sought-after keywords offer easier paths to visibility. While these may draw smaller crowds, they open doors for emerging players. The challenge lies in balancing reach and attainability, navigating the competitive landscape of search engine optimization. Success demands strategic keyword selection, weighing difficulty against potential rewards.
Several factors contribute to keyword competition, including:
– The number of websites already targeting the keyword.
– The domain authority and page authority of competing sites.
– The quality and relevance of the content competing for that keyword.
Why Keyword Competition Matters
Keywords can make or break your SEO strategy. Highly competitive ones demand substantial investment but promise greater traffic. Less contested terms offer quicker gains yet fewer visitors. Assessing competition guides resource allocation and timeline expectations. Will you need months or years to reach Google’s first page? The answer lies in your keyword choices.
A balanced approach, blending high and low-competition keywords, paves the way for enduring SEO success. Carefully weigh your options to optimise both short-term wins and long-term growth.
Factors That Affect Keyword Competition
1. Search Volume
Keywords sought frequently each month have higher search volumes. These popular terms often face fierce competition as websites vie for traffic. Yet exceptions exist. Some niche phrases, though widely searched, encounter less rivalry. Fewer businesses may target these specialized keywords, creating opportunities.
Remember, search volume alone doesn’t dictate competitiveness. Savvy marketers consider both factors when crafting strategies to reach their audience effectively.
2. Relevance to Your Business
The relevance of a keyword to your business or industry can impact how competitive it is. If a keyword is highly relevant to many businesses in a particular industry, competition will naturally be higher. For instance, a broad keyword like “best laptop” is likely to have significant competition, whereas a more specific term like “best laptop for graphic designers under $1000” may have lower competition.
3. DA and PA
Moz’s Domain and Page Authority metrics gauge website and page strength. Higher scores boost ranking potential for competitive keywords. This advantage creates a barrier for emerging sites, hampering their ability to reach top search positions. These influential indicators shape the digital landscape, determining visibility and success in search results.
4. Content Quality
Content quality reigns supreme in keyword battles. Top-ranked sites boast stellar writing, deep insights, and captivating prose. To dethrone them, your content must soar even higher. Google rewards user value above all. Flimsy, copied, or subpar material falters, regardless of keyword prowess. Outshine competitors with substance, not just strategy. Craft content that informs, engages, and elevates the user experience to climb the search rankings.
5. Backlinks
High-quality backlinks boost a website’s competitive edge. These inbound links from other sites shape keyword competition. More backlinks often mean greater authority. Smaller sites struggle to secure links from reputable sources. This challenge intensifies keyword battles. Authoritative backlinks are crucial yet elusive. Their scarcity drives up competition, making keyword dominance harder to achieve.
How to Measure Keyword Competition
1. Google Keyword Planner
Google Keyword Planner, a free Google Ads tool, offers more than just paid search insights. It categorises keyword competition as “Low,” “Medium,” or “High” based on advertiser bidding. Though this metric primarily reflects paid search dynamics, it provides a useful starting point for organic competition analysis.
2. Ahrefs Keyword Difficulty (KD) Score
From 0 to 100, Ahrefs’ Keyword Difficulty score gauges SEO competition. Low scores (0-20) signal easier ranking prospects, while high scores (50+) indicate fierce battles. This popular tool assesses keyword competitiveness by analysing backlink profiles of top-ranking pages. SEO strategists rely on Ahrefs’ KD metric to identify promising opportunities and navigate the complex landscape of search engine optimisation.
3. Moz Keyword Difficulty
Ranking difficulty for keywords is gauged by Moz’s Keyword Difficulty metric. This score weighs factors like top-ranking pages’ authority and their inbound links from unique domains. Moz’s tool also reveals competitors’ domain strength, enabling site-to-site comparisons. These insights help strategise SEO efforts and assess potential ranking challenges.
4. SEMrush Competitive Density
SEMrush’s competitive density score reveals the number of domains vying for paid ad space on specific keywords. Though primarily geared towards paid advertising, this metric offers valuable insights for organic SEO strategies. When combined with SEMrush’s keyword difficulty score – a 0-100 scale – marketers gain a comprehensive view of both paid and organic keyword landscapes.
5. Manual SERP Analysis
One of the best ways to measure keyword competition is through a manual analysis of the SERPs for your target keyword. This gives you a hands-on understanding of what you’re up against. Here’s what the process involves:
– Reviewing the top 10 results.
– Evaluating the domain authority and page authority of the top-ranking websites.
– Checking the content’s quality and the number of backlinks for these pages.
Strategies for Navigating Keyword Competition
1. Target Long-Tail Keywords
Long-tail keywords are specific phrases with lower search volume and competition. For example, instead of “smartphones,” aim for “best smartphones for students under $500.” These keywords often lead to higher sales because they match user intent closely.
2. Create High-Quality, Unique Content
To stand out in a crowded keyword space, your content must surpass existing top ranks. This involves offering detailed information, unique insights, and better-addressing user intent. Moreover, high-quality content naturally draws backlinks, improving your rankings.
3. Build a Strong Backlink Profile
Getting quality backlinks from trusted sites is key to boosting your site’s ranking for competitive keywords. You can earn these backlinks by creating valuable content like research studies, infographics, and expert interviews. Additionally, guest blogging and contacting influencers can also secure you valuable backlinks.
4. Focus on On-Page Optimisation
On-page optimisation involves SEO techniques for your website’s content and structure. Key aspects include placing keywords in headings, meta descriptions, and body content. Additionally, optimising images and internal links is crucial. These steps can enhance your visibility in competitive keyword settings.
5. Leverage Local SEO
If your business targets a specific area, local SEO boosts your regional keyword ranking. Key steps include optimising your Google My Business profile, using location keywords, and earning positive reviews. This strategy particularly benefits small and medium-sized businesses.
Conclusion
If you need better support in understanding keywords, feel free to speak with an expert SEO in Melbourne. We recommend Make My Website, a reliable SEO marketing agency in Melbourne.
TECHNOLOGY
PR Public Relation Guest Post Agency Guest Posting: A Modern Strategy for Brand Credibility and Digital Authority
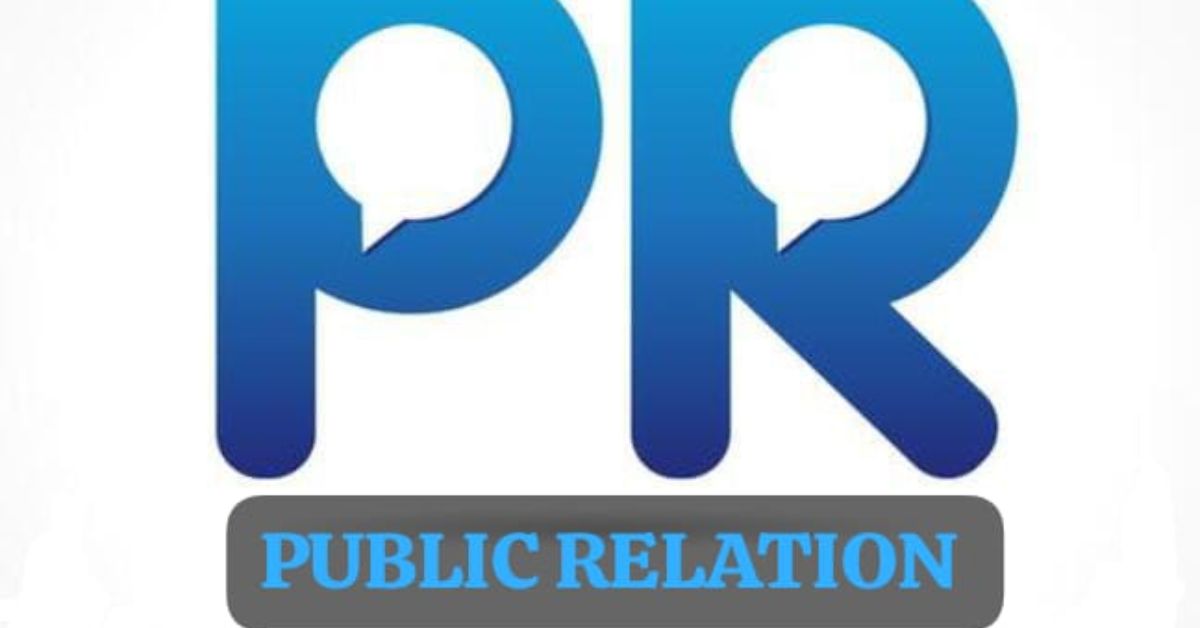
In the digital age, where online visibility directly influences brand success, PR Public Relation Guest Post Agency (PR) has evolved from traditional press coverage and event management into a more dynamic, content-driven practice. One of the most effective strategies at the intersection of modern PR and digital marketing is guest posting.
Guest posting—publishing content on external, high-authority websites—not only supports link-building and SEO goals but also plays a critical role in shaping public perception, building thought leadership, and enhancing brand trust. For professionals, startups, and enterprises alike, integrating guest posting into a PR Public Relation Guest Post Agency plan has become an indispensable tactic for long-term brand positioning.
Understanding Guest Posting in the PR Context
Traditionally, PR focused on managing the flow of information between an organization and the public. It was about getting stories into newspapers, interviews on radio, or features on TV. However, the digital shift has changed how audiences consume content. People now turn to blogs, digital publications, industry websites, and social media for insights and updates.
This shift has broadened the definition of PR. It’s no longer limited to media relations—it includes content marketing, thought leadership, influencer partnerships, and most notably, guest posting on authoritative platforms.
Guest posting in PR involves writing and publishing valuable, non-promotional content on websites that align with your industry or target audience. The goal is not just exposure, but positioning your brand or spokesperson as a credible authority, while also subtly driving traffic and improving SEO rankings through contextual backlinks.For more information please contact this email: toppublicrelation@gmail.com
Why Guest Posting Matters for Public Relations
Here’s why guest posting is a vital tool for modern PR Public Relation Guest Post Agency:
1. Establishing Thought Leadership
Credibility is currency in the digital world. When a company’s executive or representative contributes an article to a respected industry site, it reinforces their position as a thought leader. Readers trust websites they follow, so your message carries more weight when published externally than when posted on your brand blog.
Guest posting allows PR professionals to tell their story proactively, providing meaningful commentary on industry trends, innovations, and challenges—before the competition does.
2. Controlling the Narrative
Guest posts offer a powerful form of narrative control. Instead of relying on third-party journalists to interpret your press releases or statements, you get to shape your message directly. With guest posting, your voice becomes the official voice of record, helping prevent misrepresentation or dilution of the message.
This control is especially critical during product launches, rebranding efforts, crisis management, or shifts in company strategy. A well-placed article on a trusted platform can clarify your intentions, inspire confidence, and reduce misinformation.
3. Link Building and SEO
From a technical PR standpoint, backlinks are one of the strongest ranking factors in search engine algorithms. Guest posts are a natural way to earn these links, especially from high-authority domains.
When your content is published on a DA 70+ website and links back to your homepage or landing page with relevant anchor text, it improves your search engine visibility, increases referral traffic, and amplifies your online authority.
PR isn’t just about being seen in the news—it’s about being found when your audience is searching. Guest posting bridges this gap effectively.
How to Use Guest Posting Strategically in PR Campaigns
For a guest posting strategy to support your PR goals, it must be executed with precision. Below are key steps to follow:
1. Define Your PR Objectives
Are you looking to boost brand awareness? Rebuild reputation? Introduce a new product? Increase executive visibility? Your goals will shape the types of websites you target and the content themes you develop.
2. Target the Right Platforms
It’s not just about quantity—it’s about quality. Target websites that:
- Have high Domain Authority (DA)
- Are relevant to your industry or niche
- Have engaged audiences
- Accept guest contributions
Examples include platforms like Entrepreneur, Inc., Business Insider, or niche-specific blogs and publications with loyal readerships.
3. Create Valuable, Non-Promotional Content
Guest posts should never be overt sales pitches. Focus on educating, informing, or solving a problem. Showcase your expertise subtly while delivering genuine value. Content that reads like an article in Forbes, not an ad, will resonate better and be more widely accepted.
4. Craft a Strong Author Bio
The author bio is where you can place a branded backlink and provide credentials. It should reflect the authority of the spokesperson and give readers a clear reason to trust or follow the company.
5. Track Impact and ROI
Track metrics like:
- Referral traffic from guest post backlinks
- Organic keyword rankings
- Brand mentions and citations
- Media coverage triggered by guest post visibility
- Lead generation and conversions
These indicators help measure the real PR impact of guest posting campaigns.
Best Practices for Public Relations Guest Posting
To maximize the benefits of guest posting within your PR strategy, keep these best practices in mind:
- Personalize your outreach:Avoid mass-pitching editors. Tailor your pitches to show familiarity with the site’s tone and topics.
- Stay consistent:Publish regularly, not sporadically. Consistency builds recognition.
- Update your posts:Offer evergreen content, but revisit and refresh when necessary.
- Leverage social media:Share guest posts across LinkedIn, X (Twitter), and Facebook to extend reach.
- Build relationships with editors:Guest posting can open doors to broader PR opportunities like interviews, collaborations, and features.
The Future of PR: Content-Led Brand Building
The era of PR being reliant solely on press releases and journalists is long gone. Brands are now media companies, and their content is their currency. Guest posting fits perfectly into this model, offering a direct channel to communicate with audiences, control messaging, and build digital authority.
In the coming years, we’ll continue to see the fusion of PR, SEO, and content marketing. Agencies and internal teams that understand how to craft compelling guest posts and secure premium placements will lead the conversation in their industries.
Moreover, as AI and automation evolve, the human element—trust, credibility, and storytelling—will matter more than ever. Guest posting remains a tool where human perspective and professional authority can truly shine.
Conclusion
PR Public Relation Guest Post Agency today is a multidimensional effort that includes strategic content distribution, relationship-building, and digital visibility. Guest posting is a core pillar of this strategy—one that not only enhances online authority and improves SEO but also builds real, lasting brand trust.
Whether you’re launching a brand, repositioning a business, or strengthening your digital footprint, guest posting should be an integral part of your PR toolkit. It delivers value beyond a single post—contributing to your brand’s voice, influence, and credibility in a way few other tactics can.
TECHNOLOGY
Why Every E-commerce Store Needs an AI Chatbot Development Company in 2025?
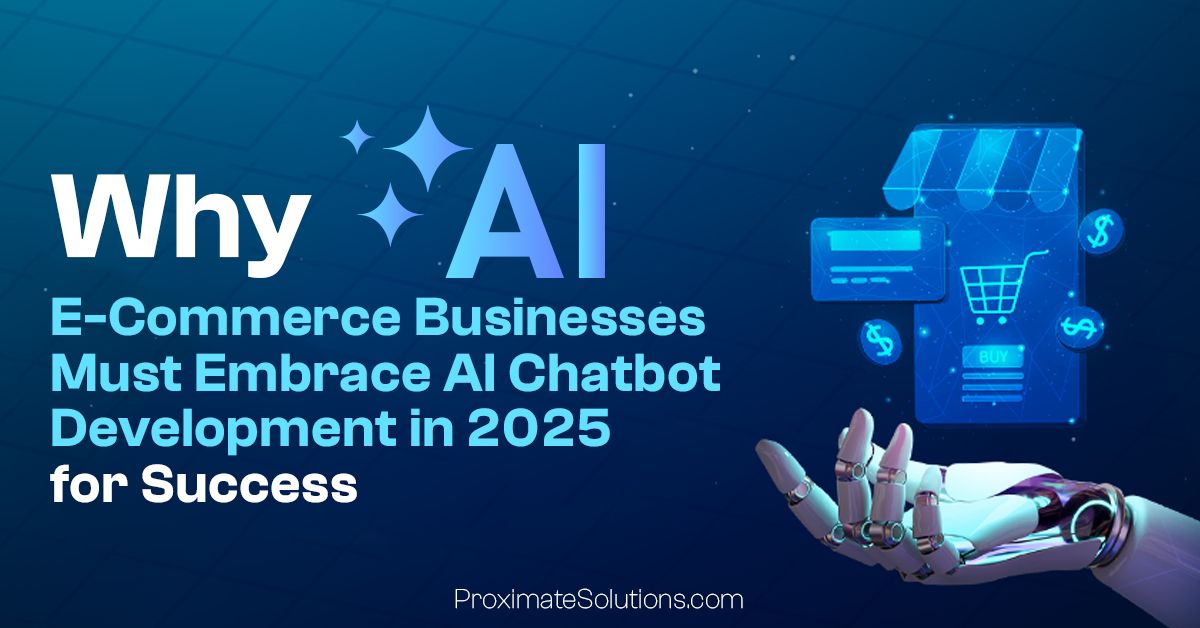
The Future of E-commerce Is AI-Driven
In 2025, customer expectations are evolving faster than ever. E-commerce brands are now competing on speed, personalization and round-the-clock availability. That’s where an AI Chatbot Development Company steps in. With AI transforming customer service, these companies enable businesses to deliver smarter, faster and more human-like support.
Today, 80% of retail and e-commerce businesses are either using or planning to implement AI chatbots. Additionally, the AI chatbot market in e-commerce is expected to reach $2.1 billion by 2032, driven by its ability to streamline operations, reduce costs and boost customer satisfaction.
Furthermore, an AI Chatbot Development agency equips brands with intelligent, automated support systems trained to sound like their brand, respond instantly and retain customer loyalty. Thus, for any business owner tired of answering repetitive questions, chatbots offer the perfect solution.
What Does an AI Chatbot Development Company Offer?
An AI Chatbot Development agency builds smart virtual assistants tailored for e-commerce platforms. These chatbots perform essential functions while saving businesses time and money. Additionally, here’s what they typically offer:
24/7 Customer Support: AI chatbots are always available to help since they never sleep.
Product Recommendations: They personalize suggestions based on browsing behavior.
Order Tracking: Customers get real time updates without contacting human agents.
Multilingual Communication: Breaks language barriers for global markets.
Cart Recovery Campaigns: Reminds customers to complete purchases.
Instant Query Handling: From FAQs to refund policies, bots manage it all efficiently.
Thus, by partnering with a professional AI Chatbot Development Company, brands receive custom built solutions that align with their tone, branding and goals.
How AI Chatbots Are Transforming E-commerce Customer Support
E-commerce customers expect quick responses and relevant solutions. That’s where AI chatbots shine. Additionally, these bots are trained on a company’s knowledge base, FAQs and customer workflows, providing accurate answers instantly. Thus, here’s how they transform customer support
Faster Response Times: Chatbots answer within seconds, reducing wait time.
Scalability: Handle thousands of conversations without needing more staff.
Brand Consistency: They reflect your tone and speak like your business.
Reduced Human Errors: AI systems ensure consistent and factual responses.
Lower Support Costs: Businesses save up to 30% in customer service costs.
Furthermore, a trusted and experienced AI Chatbot Development Company like Proxmate Solutions ensures bots can grow with your business and adapt to changing customer needs. That flexibility is very important in a competitive market.
Why Every E-commerce Business Needs AI Chatbots in 2025
Customer behavior in 2025 demands innovation. Today’s consumers use voice search, prefer messaging over calling and expect instant gratification. AI chatbots meet these demands by integrating seamlessly into websites, apps and messaging platforms.
Furthermore, here are the top reasons to invest in chatbot development
Consumer Trends: Most customers prefer messaging platforms over emails or calls.
Conversion Boost: Bots help customers check out which boosts sales.
Lead Qualification: Chatbots gather user data and segment customers.
Customer Retention: Personalized responses improve satisfaction and loyalty.
Voice Search Optimization: Modern bots work well with voice commands.
This is why hiring an AI Chatbot Development Company is no longer optional. It’s a strategic necessity.
Why Choose Proximate Solutions as Your AI Chatbot Development Company?
With over 20+ years of experience, Proximate Solutions stands out among AI chatbot providers. They are committed to quality, innovation and results-driven services. Whether you’re a startup or an established enterprise, their custom chatbot solutions fit businesses of all scales.
Reasons to hire Proximate Solutions
Proven Experience: Decades of expertise in AI and automation.
Sales-Focused Strategy: They build chatbots that convert, not just communicate.
Affordable Global Services: Competitive rates with top-tier service quality.
Always Up-To-Date: They embrace new AI trends to keep you ahead.
Custom Training: Their bots are trained on your brand tone, FAQs and workflows.
Furthermore, tired of answering repetitive customer queries? Proximate Solutions creates AI-powered chatbots that retain customer engagement, reduce response time and sound exactly like your brand.
Key Benefits of Hiring an AI Chatbot Development Company
Working with an AI Chatbot Development agency offers distinct advantages. Here are the key benefits that e-commerce businesses gain:
Increased Customer Satisfaction: Bots resolve issues quickly and accurately.
Boosted Efficiency: Agents can focus on complex cases while bots handle routine queries.
High ROI: Chatbots reduce support costs and drive conversions.
Brand Loyalty: Personalized interactions build stronger customer relationships.
Seamless Integration: Bots can be added to Shopify, WooCommerce, Magento and more.
Thus, choosing the right partner ensures you make the most of your AI investment. That’s where Proximate Solutions proves its value repeatedly.
A Look at the Future: AI Chatbots and Rising Expectations
By 2025, customers will expect businesses to be available 24/7, responsive and conversational. AI chatbot integration addresses all of these demands.
As the AI market grows, businesses that adopt early will have a competitive edge. AI-powered bots will not just assist but anticipate customer needs, becoming virtual shopping assistants.
Furthermore, future-ready e-commerce brands will use AI to:
- Predict customer preferences
- Handle high volume shopping events
- Improve post purchase engagement
- Offer hyper personalized support
Moreover, brands can successfully adjust to these developments with the help of professionals like Proximate Solutions. Their strategic approach to chatbot development ensures long term growth.
Conclusion: Build the Future of Customer Support Now
It’s very important to match customer expectations in the rapidly evolving world of e-commerce today. AI chatbots do more than answer questions; they build trust, drive sales and elevate brand experience. Thus, the businesses that recognize this shift and partner with an expert AI Chatbot Development Company will lead the way.
Furthermore, Proximate Solutions is one of the best choices to start this journey. With a proven track record, global reach and sales-focused strategies, they help e-commerce stores thrive in the AI-powered era.
Thus, don’t let your brand fall behind. Invest in AI chatbot solutions that speak your brand’s language, serve your customers 24/7 and power your business into the future.
Frequently Asked Questions (FAQs)
- What is an AI Chatbot Development Company?
It’s a company that creates intelligent chatbots using artificial intelligence to automate customer support and sales processes.
- Why do e-commerce stores need AI chatbots in 2025?
Customer expectations demand instant responses and 24/7 support which AI chatbots provide efficiently.
- How much does it cost to hire an AI Chatbot Development Agency?
Costs vary, but companies like Proximate Solutions offer competitive pricing tailored to your business size.
- Can AI chatbots increase my e-commerce sales?
Yes. They assist during purchase decisions, offer upsells and remind customers to complete abandoned carts.
- Are AI chatbots compatible with Shopify or WooCommerce?
Absolutely. An experienced AI Chatbot Development agency can integrate bots into all major platforms.
- How do AI chatbots personalize customer experiences?
They use browsing history, previous orders and user preferences to offer tailored product suggestions.
- How secure is customer data with AI chatbots?
Top companies follow strict data protection protocols and ensure GDPR and CCPA compliance.
TECHNOLOGY
Using Dynamics 365 Customer Engagement to Build Stronger Customer Relationships
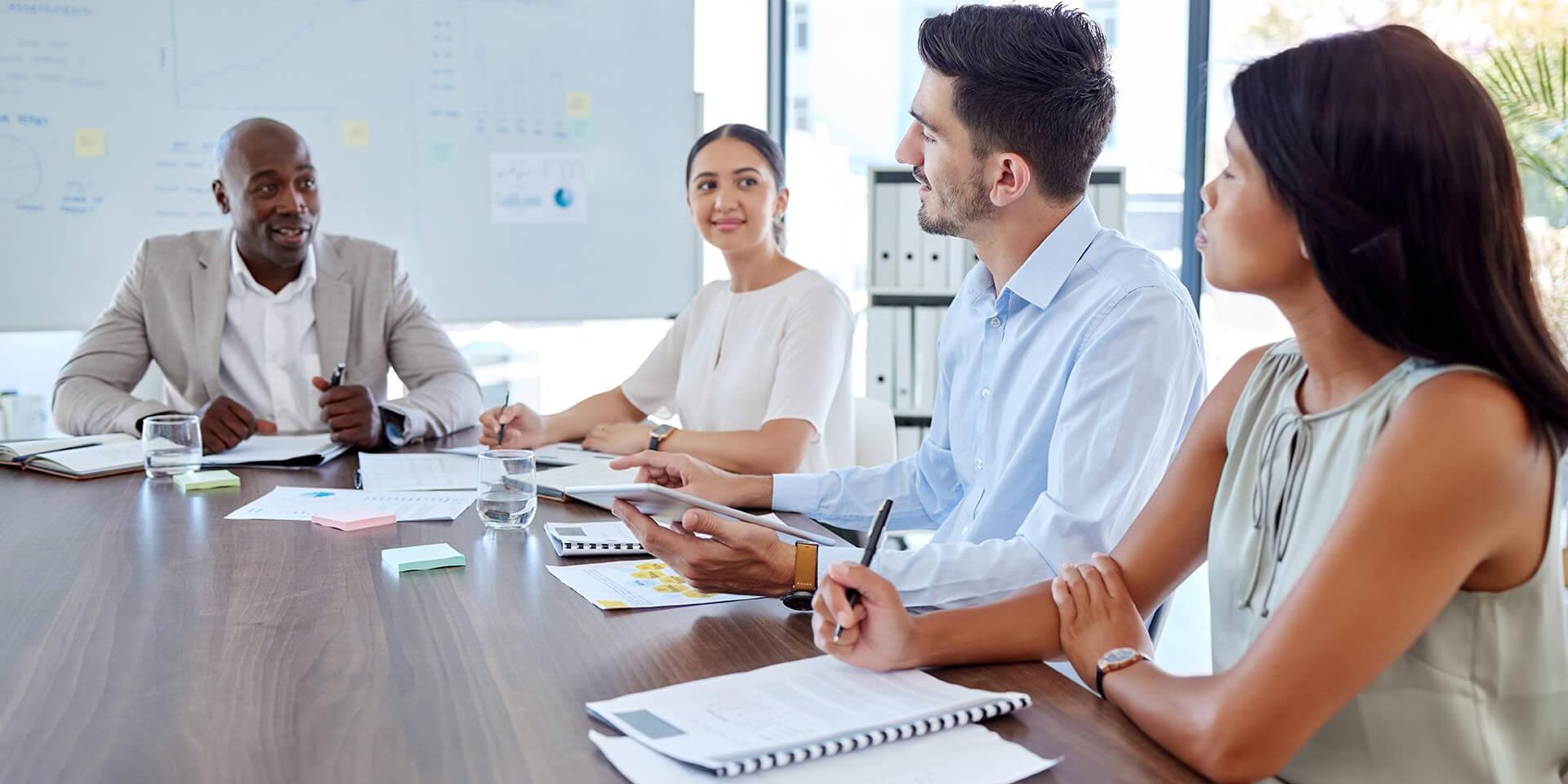
In today’s ultra-competitive business environment, having a great product or service is no longer enough. Customers expect personalized experiences, quick responses, and proactive engagement. The brands that stand out are the ones that truly understand their customers and build relationships that go beyond the transaction.
That’s where Dynamics Customer Engagement (part of Microsoft Dynamics 365) comes in. This powerful suite of applications helps businesses manage interactions and elevate every touchpoint—from sales and marketing to service and support.
In this post, we’ll explore how Dynamics 365 Customer Engagement enables businesses to build stronger customer relationships by unifying data, automating processes, and delivering personalized experiences.
What Is Dynamics Customer Engagement?
Dynamics 365 Customer Engagement (D365 CE) is a collection of applications within Microsoft’s Dynamics 365 ecosystem designed to manage customer-facing functions. These include:
- Sales
- Customer Service
- Marketing
- Field Service
- Project Service Automation
These apps help businesses gain a 360-degree view of customers, track interactions, automate follow-ups, and provide consistent, data-driven experiences at every customer journey stage.
Key ways Dynamics Customer Engagement builds stronger relationships
1. A Unified view of the customer
Nothing damages a relationship like fragmented communication. With Dynamics Customer Engagement, all customer data—past purchases, support tickets, email interactions, preferences—is unified in one place. This gives your teams complete visibility into who the customer is and what they need.
Sales, marketing, and service teams can all work from the same playbook. This ensures no customer falls through the cracks and every conversation feels informed and consistent.
2. Personalized Engagement at Scale
Customers want to feel understood, not marketed to. Dynamics Customer Engagement empowers you to deliver hyper-personalized experiences by leveraging AI-powered insights and behavioral data.
With dynamic segmentation in the marketing app, for example, you can send tailored messages based on a customer’s interests, buying history, or activity level. The sales team can use predictive insights to recommend the right next steps. Support agents get context about previous issues so they don’t have to ask customers to repeat themselves.
This level of personalization shows customers that you’re not just managing a database—you’re invested in the relationship.
3. Automated, Timely Interactions
Timeliness is key in maintaining strong relationships. Whether it’s a sales follow-up, service update, or birthday greeting, Dynamics Customer Engagement helps you automate communication without losing the human touch.
You can set up workflows to trigger emails, assign tasks, or escalate issues automatically. This ensures customers are always in the loop and feel valued, without overwhelming your team with manual follow-ups.
Marketing automation, in particular, lets you nurture leads with the right content at the right time, increasing trust and conversion rates.
4. Proactive Customer Service
Great relationships are built on trust, often from solving problems before they escalate.
With Dynamics Customer Engagement, your service teams can become proactive instead of reactive. Built-in dashboards and AI-driven insights can flag potential issues early, allowing you to reach out to customers before they complain.
The system can also suggest the next best actions, knowledge articles, or even automatically route cases to the most qualified agent. This reduces resolution time and boosts customer satisfaction.
5. Mobility and Accessibility
Today’s workforce is mobile, and so are customers. Dynamics CE is accessible across devices, ensuring that your team can engage with customers wherever they are—whether it’s on the sales floor, in the field, or working remotely.
Sales reps can pull up real-time customer data before a meeting. Service agents can respond to queries from a tablet. Field technicians can update job status on-site. That level of connectivity keeps your team aligned, informed, and ready to serve.
Real-World Example: Turning Data into Delight
Let’s say you run a mid-sized B2B company. You’ve been struggling with customer churn and inconsistent service experiences. By implementing Dynamics Customer Engagement, you’re able to:
- Sync sales, service, and marketing teams onto one platform
- Segment customers by industry and behavior
- Automate onboarding emails and product tips
- Flag inactive accounts for proactive outreach
- Equip support agents with detailed customer histories
Over six months, your churn rate drops, customer feedback improves, your team feels empowered, and most importantly, your customers feel like they matter because every interaction reinforces that belief.
Choosing the Right Dynamics CE Modules
Depending on your goals, you might not need the entire Dynamics suite. Here’s a quick guide:
- For Relationship Management & Sales: Start with Dynamics 365 Sales.
- For Personalized Marketing Campaigns: Use Dynamics 365 Marketing.
- For Omnichannel Customer Support: Go with Dynamics 365 Customer Service.
- For On-site Services: Consider Dynamics 365 Field Service.
Each module can work independently or as part of a connected solution, giving you flexibility as your business evolves.
Final Thoughts: Relationship-Building in the Digital Age
In an age where customers are bombarded with choices, loyalty comes down to how they feel about your brand. Do they feel heard? Understood? Valued?
Dynamics Customer Engagement helps answer those questions with a resounding “yes.” Combining unified data, intelligent insights, and personalized automation transforms how you connect with customers, from one-off transactions to long-term partnerships.
If building stronger relationships is a priority for your business—and it should be—investing in the right tools like Dynamics Customer Engagement isn’t just a tech decision. It’s a growth strategy.
-
TECHNOLOGY1 year ago
Elevating Game Day Eats: A Guide to Crafting Crowd-Pleasing Sliders
-
ENTERTAINMENT1 year ago
wave_of_happy_: Your Ultimate Guide
-
FASHION1 year ago
GPMsign Fashion: Redefining Style with Purpose
-
TECHNOLOGY1 year ago
Trader Joe’s Dayforce: Revolutionizing Workforce Management
-
FOOD1 year ago
Altador Cup Food Court Background: A Culinary Extravaganza Unveiled
-
SPORTS1 year ago
Score Chaser Sporting Clays: A Thrilling Pursuit of Precision
-
HOME IMPROVEMENT10 months ago
What Kitchen Renovation Companies Offer Beyond Basic Remodeling
-
NEWS1 year ago
Nyl2 Kemono: Unveiling the World